Case Study: Successful Logistics Optimization for a Local Business
Introduction to Logistics Optimization
In the rapidly evolving world of logistics, local businesses often face challenges in managing their supply chains efficiently. This case study delves into the successful logistics optimization of a small business, transforming its operations and driving significant growth.
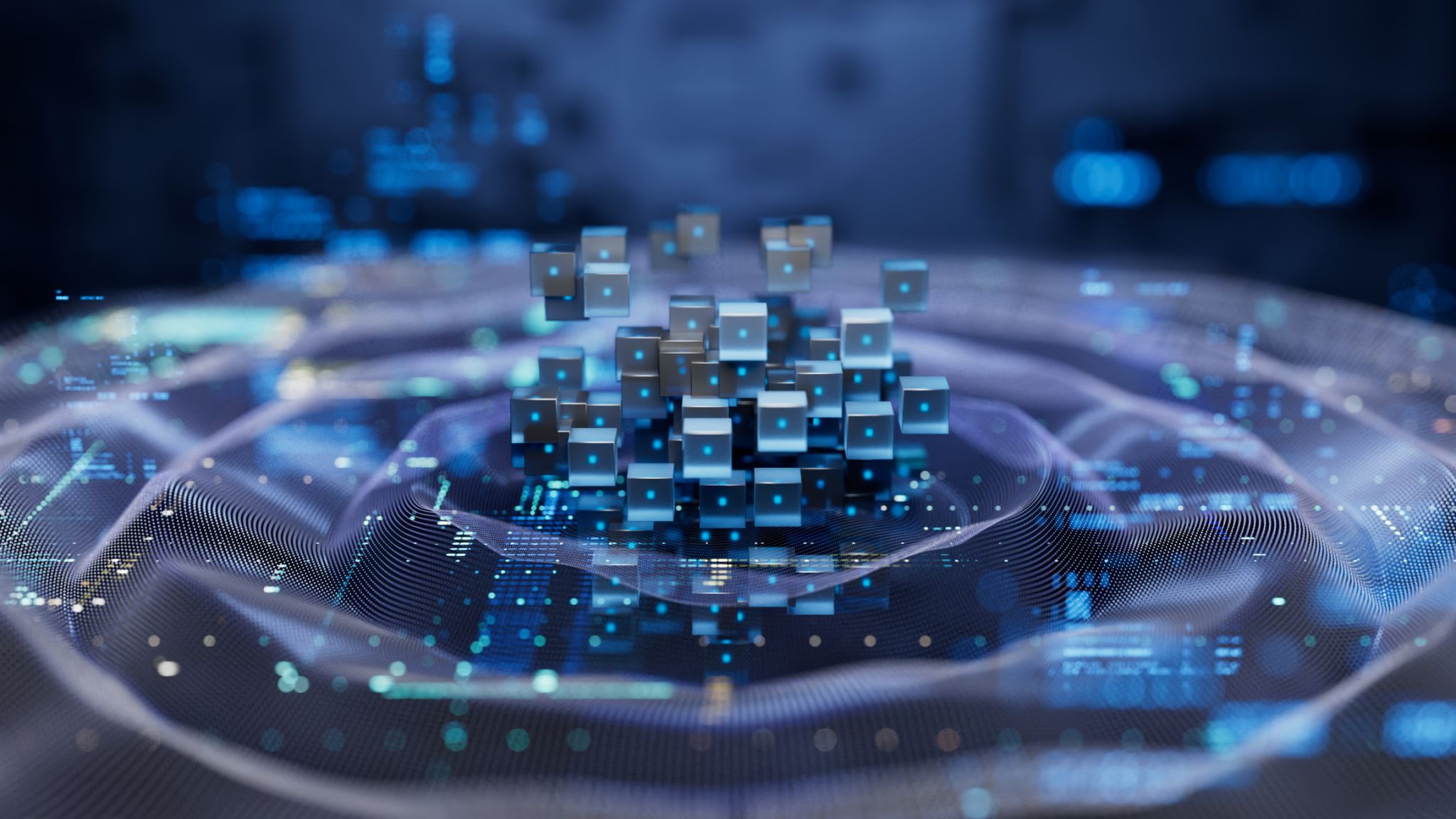
The Challenge
The business, a family-owned grocery store, faced several hurdles in its logistics processes. With increasing competition and consumer expectations, the store struggled with inventory management, timely deliveries, and cost control. These issues led to frequent stockouts and overstock situations, negatively impacting customer satisfaction and profitability.
The primary objective was to streamline operations, reduce costs, and enhance customer experience. The business decided to overhaul its logistics strategy to better meet these goals.
Implementing Strategic Changes
To address these challenges, the business partnered with a logistics consulting firm. The first step was conducting a comprehensive analysis of the existing supply chain. This included evaluating suppliers, distribution methods, and inventory practices. The insights gathered helped in formulating a new strategy.
- Supplier Collaboration: Strengthening relationships with key suppliers was crucial. By improving communication and establishing long-term contracts, the business ensured better pricing and reliability.
- Technology Integration: Implementing an inventory management system provided real-time data, enabling more accurate demand forecasting and reducing instances of understocking or overstocking.
- Route Optimization: Using advanced software, delivery routes were optimized to minimize fuel consumption and delivery times.
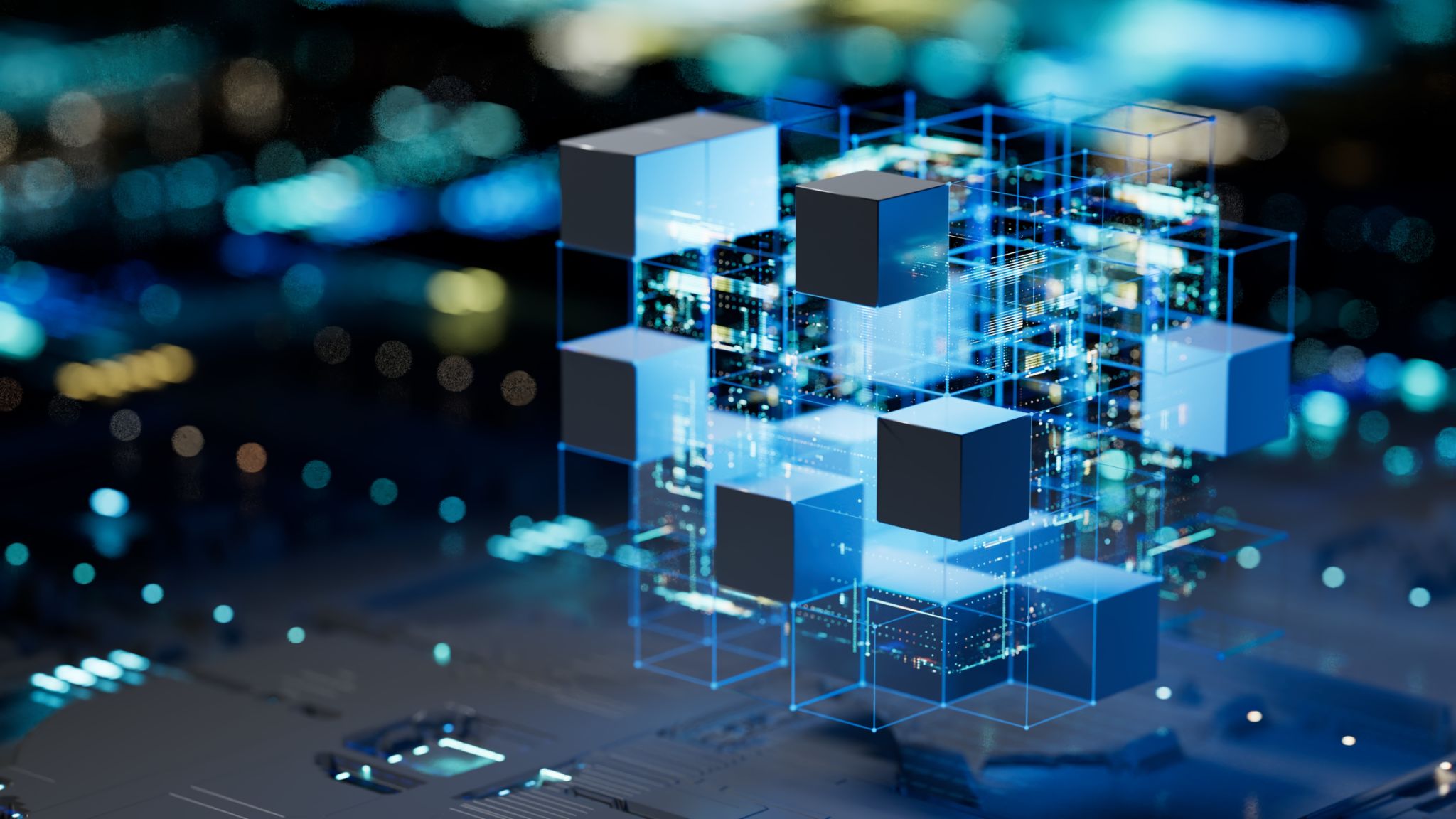
Results and Impact
The changes led to remarkable improvements in the business's logistics operations. Inventory accuracy improved by 30%, significantly reducing holding costs. Customer satisfaction soared with on-time delivery rates increasing by 25%. The implementation of technology not only streamlined operations but also provided valuable insights for future decision-making.
Cost savings were evident as well. By optimizing routes and collaborating closely with suppliers, the business saved approximately 15% on logistics expenses annually. This reinvestment into the business fueled further growth and expansion opportunities.
Lessons Learned
This case study highlights several key takeaways for other local businesses aiming to optimize their logistics:
- Data-Driven Decisions: Leveraging technology for real-time data collection and analysis is vital for informed decision-making.
- Supplier Partnerships: Building strong relationships with suppliers can lead to better terms and more reliable service.
- Continuous Improvement: Logistics optimization is an ongoing process that requires regular evaluation and adaptation.

Conclusion
The successful logistics optimization of this local grocery store demonstrates that even small businesses can achieve substantial improvements with the right strategy and tools. By focusing on collaboration, technology, and continuous improvement, businesses can enhance efficiency, reduce costs, and ultimately deliver better value to their customers.
This case study serves as an inspiration for other local businesses seeking to innovate and improve their logistics operations to stay competitive in today's fast-paced market environment.